FY08 MCON P-431 Alpha and Bravo Wharf Improvements at the Commander Naval Region Marianas, Polaris Point – Guam
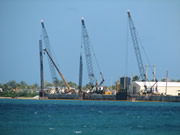
Bravo wharf was turned over to the Navy early on November 30, 2007 along with its associated utilities and support facilities which also serve Alpha wharf. Alpha wharf itself was turned over on May 16, 2008 two months before CCD.
Wharf Upgrades – The existing Alpha and Bravo wharves were upgraded through the construction of a new 1,371′ sheet pile bulkhead offset and parallel to the existing wharves and tied back with walers and tie-rods to a composite anchorage system of battered 80′ to 120′ long HP14x89 steel h-piles and poured in place concrete anchor block located inland. The resulting annular space between the existing wharves and new sheet pile bulkhead wall was filled with 5,500 CY of tremied lean concrete and then capped by a 6’Wx9’H poured in place concrete beam using 3,000 CY of 5,000PSI marine concrete with ASTM 935 epoxy coated steel reinforcement. The same structural scheme was used to extend and reclaim the north end of Bravo wharf an additional 152′. It should be note that this was the first time marine concrete was used anywhere on Guam. It is also the first time fly-ash was imported and used in a concrete mix on island.
Construction of the 1,371′ sheetpile bulkhead required Black to drive 216 each 86.5′ long single and double king piles and 216 each 73.0′ long intermediate sheet pile pairs weighing from 5.12 tons to 16.1 tons each for a total weight of 3,267 tons. The seaward face of each king and sheet pile was sandblasted and coated with coal tar epoxy on site prior to installation. Similarly, Black drove 604 h-piles for the composite anchorage system. The h-piles weighed from 3.6 tons to 5.3 tons each for a total weight of 3,151 tons. Of special note is the fact that Black had to special charter US flagged tug and barges to deliver the kings and sheet piles to Guam from their point of manufacture in Belgium and for the h-piles from South Korea since no US commercial carrier has service between Guam and these locations.
In addition to the coal tar epoxy coating the new kings and sheets are protected from saltwater corrosion by 156 each 540# aluminum galvanic anodes. The galvanic anode corrosion protection system includes 11 anode and reference electrode test boxes.
Black placed approximately 8,000CY of surge rock and engineered fill to reclaim the 1,800SY Bravo extension after its sheet pile bulkhead and composite anchorage system were completed.
Due to the buried location of the concrete anchor blocks and tie-rods approximately 18,000 CY of existing soil and demolition debris were excavated and removed from the landward areas at Bravo and Alpha wharfs. Approximately 8,000 CY of the excavated material was screened and reused as general fill to sub base level. Roughly 9,000 CY of base course was placed for the 22″ thick compacted base layer beneath the 12,400 SY of 6″ thick AC paving.
The paving for the new Bravo extension was designed for 90T crane and 20T forklift loads. The Bravo extension received a 16″ thick concrete deck slab which required 800 CY of 650 flex concrete.
The remaining wharf improvements included both new and refurbished mooring bollards and double bits, galvanized steel bull rail curb guards, hanging epoxy coated galvanized steel fender panels, stainless steel ladders, oil boom rings, and brow gangway platforms.
New Utilities and Support Facilities – As part of the first (Bravo) phase of the project, Black was required to construct all of the back of wharf utilities and support facilities which serve both Bravo and Alpha wharfs. These included construction of new fire pump and generator buildings, the 1,800SY Bravo extension parking lot, chain link fencing, new fire and water main and associated distribution piping, hydrants, and new water/sewer/ and BOW ship service risers, overhead electrical work and building power service riser, two 75KVA pad mounted power transformers and buried electrical ductwork, power and control wiring, perimeter security lighting, new wharf operations lighting, relocation of two existing ship power mounds, and the temporary bypassing, removal, and reinstallation of existing and new water, sewer and BOW piping as needed to maintain service to at least one wharf at all times.
The 1,700SF fire pump and 600 SF generator buildings were of single story, concrete slab foundation, CMU block wall, and concrete roof construction. Both concrete roofs were constructed with precast-prestressed panels and topping. Both buildings have new asphalt driveways and chain link breezeway gates. At the request of the Navy, the interior walls of the two buildings were left unpainted. The exterior wall and floors of both buildings received latex paint and epoxy deck coating respectively. An elastomeric waterproofing system was used to coat their roofs.
The fire pump building houses two 1,500 gpm 125 HP diesel engine driven fire pumps, a 250 gpm 40HP electric jockey pump and related controller and piping. The building is secured by a chain link fence perimeter. The generator building contains the 50KW standby diesel engine electric generator used to power the perimeter security and wharf operations lighting during power outages.
Black installed 9,500LF of 16″ through 6″ fire water mains and related valving, hydrants and ships service risers in the back of wharf area and along Bravo and Alpha wharfs.
Black installed 19 perimeter security light poles, fixtures and related conduit and wiring in the back of wharf areas. Similarly four 60′ and one 100′ steel poles for Bravo wharf operations lighting and Alpha lightning protection system were installed along with their light fixtures and associated wiring.
Dredging – The project scope required the construction of two confined disposal facilities (CDF) to contain dredged material and the dredging of the Inner Apra Harbor entrance channel and turning basin to an elevation of EL-40 feet (EL-12.2m) MLLW in order to provide sufficient draft for the Seawolf and Ohio class submarines to enter the harbor and berth at Bravo wharf. Total material dredged for the project was 188,600 CY.
Construction of the CDFs involved the clearing and grubbing of approximately 80,000 SY for CDF#2 and 35,000 SY for CDF#1. Once this was accomplished 6′ high earthen berms with 2H: 1V side slopes were constructed around the perimeter of the CDFs to contain the dredge material. The exterior slopes of the berms are vegetated to control erosion. The combined capacity of the two CDFs in their current configuration is approximately 195,000 CY.
Material dredged from the harbor was unloaded from shuttle barges by excavator into sealed dump trucks at the Uniform wharf transfer facility and hauled to the CDF’s for disposal. Per contract requirements all dredge materials were hauled in sealed dump trucks to prevent spillage on to Uniform wharf and base roadways.
The transfer facility at Uniform wharf and the CDFs are provided with truck tire wash down areas to prevent dredged material from being tracked on to the wharf and base roadways when the dump trucks travel between the transfer facility and the CDF’s.
A barge mounted 120T excavator with 70 foot extended boom and 5 material shuttle barges were used to dredge the entrance channel and turning basin and transport the material to the Uniform wharf unloading area. A GPS/SeaTools dredge position and depth monitoring system was used to minimize over and under dredging.
To protect the environment, a 30′ deep perimeter silt curtain suspended from a floating steel frame attached to the dredge barge was used to encircle and contain the suspended silt within the excavator’s action area. Dredged material was emptied into a material shuttle barge tied alongside the dredge barge. Once the shuttle barge was full it was pushed by workboat to Uniform wharf where it was enclosed with a silt curtain and then unloaded into sealed dump trucks for transport to the CDF’s. In the meantime another material shuttle barge was brought alongside the dredge barge for loading. This cycle continued throughout the dredging operation.
Water quality monitoring was conducted periodically throughout the day and whenever silt plumes were observed with a turbidimeter to insure that turbidity levels outside the silt curtains remained within acceptable limits.
Notable Features:
-
First use of marine concrete with flyash on Guam.
-
Work conducted in two phases with temporary bypassing of utilities to keep one wharf operational to the maximum extent possible while the other wharf is upgraded.
-
Bravo Wharf and related dredging turned over 1 month early on Nov. 30, 2007 and Alpha Wharf turned over 2 months before CCD in May 16, 2008.
[hr]